What Is Face Milling?
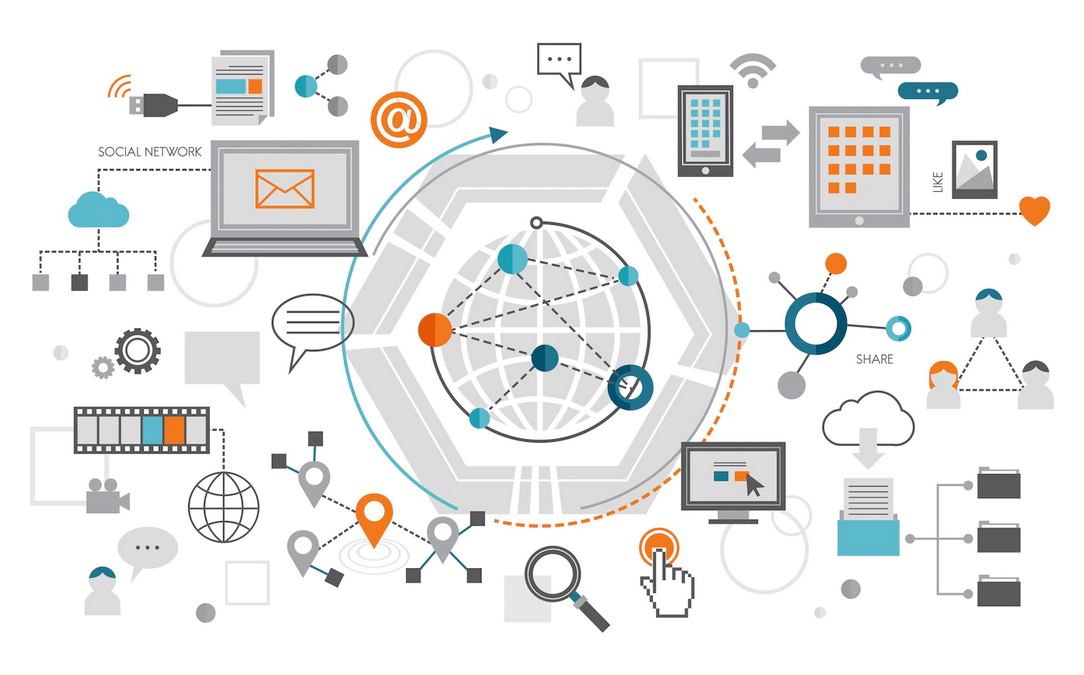
- Face Milling Machines
- Face Milling
- Simulation of face and end milling operations
- Face and Peripheral Milling
- Slotting Machine
- The 45 and 90 degree cutter
- The Role of Insert Wear and Failure in Optical Devices
- The role of the milling centres in machining
- The work of an end milling cutter
- Metal removing machine
- MeshCam - A Simple Toolpath for 3D Profiling
Face Milling Machines
Face milling machines can be used in a variety of industrial and home applications. They are used to shape wood and consumer goods in manufacturing settings. Face milling is used to cut a lot of parts in electronics and machine parts.
Face Milling
Facing milling is a milling operation in which the cutting tool's axis turned to make a surface. Which is the best milling tool? The face mill is the most common cutter used for face milling, while shell mills and fly cutter can also be used.
The face milling operations include general face milling, high face milling, heavy-duty face milling and finishing with inserts. Face mills are used to mill a face on a plate or bar. The end of the cutter is what cuts face milling.
The multiple teeth on the cutter can distribute the chip load and the teeth on the cutter's periphery can complete almost all of the cutting efficiently, when the cutter is properly ground, the face teeth remove a small amount of stock which is left because of the springing of the workpiece or cutter, 3. The cutting is accomplished by the peripheral teeth of the cutter, which are the axis of the milling cutter, and in face milling, the cutting is done by the flat face of the milling cutter.
5. In face milling, the cutting is done by the peripheral teeth and teeth on the face of the cutter, and the finishing operation is done by the peripheral teeth and teeth on the cutter. 7.
Simulation of face and end milling operations
Planing and shaping are used in woodworking, but not as often as metal cutting. They are single point cutting processes and have been displaced by high speed milling operations. The tool is fed across the workpiece to provide relative motion in a planing operation.
The tool reciprocates across the work. Small or medium size parts are usually shaped. When a hole exists, tapping is used to form the internal threads.
A threading tool is fed into a hole drilled in a previous operation by one of the drilling processes described earlier. The simulation system has been verified for both face milling and end milling operations. The end milling results are shown next.
The surface roughness is measured after face milling. The surface is affected negatively by the increased frequencies of the face milling. The surface roughness increases up to 62% compared to the reference surface.
3.3.1.7. The metal is removed by means of teeth on the cutter's circumference. It is rarely used to make large flat surfaces.
Face and Peripheral Milling
Depending on where the cut is, milling operations can be classified as face or peripheral. The milling cutter is a rotating cutting tool that is used to remove material from a piece of metal. The milling cutter presses against the surface of the piece of metal, grinding away some of the material.
Slotting Machine
Slotting machine is explained. The slotter is a type of machine tool that is similar to a shaper. It may be considered a shaper. The machine is running.
The surface of the milling tool is parallel to the axis of the cutter but in face milling it is at the right angle. Depending on the cutter's angle of view, peripheral milling can be used for both formed and flat surface. The face portion of face milling provides finishing action, unlike the peripheral portions of the teeth.
The 45 and 90 degree cutter
Be careful where you use 45 and 90 degree cutter. A well supported piece of metal will not fit under a 45 degree cutter. A 90 degree cutter will produce a more consistent cut and the decrease in chatter will extend the life of the cutter.
The Role of Insert Wear and Failure in Optical Devices
Evaluating insert wear and failure modes can be important. Everything that happens to an insert is explained. The sign of thermal stress is the comb cracks, which are a tell-tale sign.
The role of the milling centres in machining
The milling centres change tools and perform cutting. Various tools are used during the process of creating a finished product from a block of metal. Modern machining centres do not use slab mills.
They are still used with manual milling machines. That is also why slab milling is called surface milling. Face mills are better for cutting.
Fly cutter bits are often made by a shop rather than being bought from stores. Cutting ceramic tools are prone to cracking when used in high temperatures. They are not suitable for making steels.
A short tool life is expected. The properties of milling machine tools such as cemented carbide make it a step closer to high performance milling. They are a more cost-effective choice in the long run.
The work of an end milling cutter
The work is fed against the cutter to cut the grooves on the work surface after the end milling cutter is fixed on an arbor.
Metal removing machine
The metal removing operation a milling machine uses the working principle of the milling machine. The work is mounted on a machine and then on a machine's revolving multi teeth cutter. The work was fed slowly past the cutter.
The work can be fed in a variety of directions. The cutter teeth remove metal from the work surface to make a shape. The size of the milling machine is determined by the dimensions of the maximum length of the longitudinal, cross, and vertical travel of the table and the working surface of the machine.
The image shows the typical size of a milling machine. The machine should be specified in addition to the above dimensions, as well as the number of feeds, power, and net weight. The column and knee type machine is the most used milling machine for general shop work.
The table is mounted on the knee-casting and then on the vertical slides of the main column. The vertical column is adjusted at angle by the clamped head. The milling cutter can be fixed on the spindle to work on different surfaces.
The work can be adjusted relative to the work on the machine. The table is mounted on the bed. The table movement is restricted to a right angle to the axis with no provisions for cross or vertical adjustment.
MeshCam - A Simple Toolpath for 3D Profiling
2D Profiling is a common toolpath and is the lowest common denominator. There are programs that do nothing but follow a line from a file, which gives ultimate flexibility at the cost of at least some semblance of a user experience. You want to convert the entire interior of the pocket to chips.
If the middle starts flopping around and jams the tool, you should just make the outline and hope the middle falls out. There are many different toolpaths for 3D Profiling. Some are not common in the 3D Profiling world.
Some of them borrow a bit from their 2D cousins, for example, adaptive 3D clearing allows HSM toolpaths for 3D Profiling. It is more important to break roughing and finishing into two different operations and choose the appropriate toolpaths for each. Roughing is all about removing the majority of the material as quickly as possible, but what it leaves behind may not be as close to the finished work as you might think.
The stair step is shown in a 3D roughing pass. It is important to how the cutter enters the cut to ensure a good tool life and surface finish. There are lots of entry options in the most popular CAM packages.
One of the most common ways to ramp down is with a plunge. If you are using MeshCam, it makes it simpler to use a 3D surface toolpaths for everything. It works well.









X Cancel