What Is Hot Zinc Spraying?
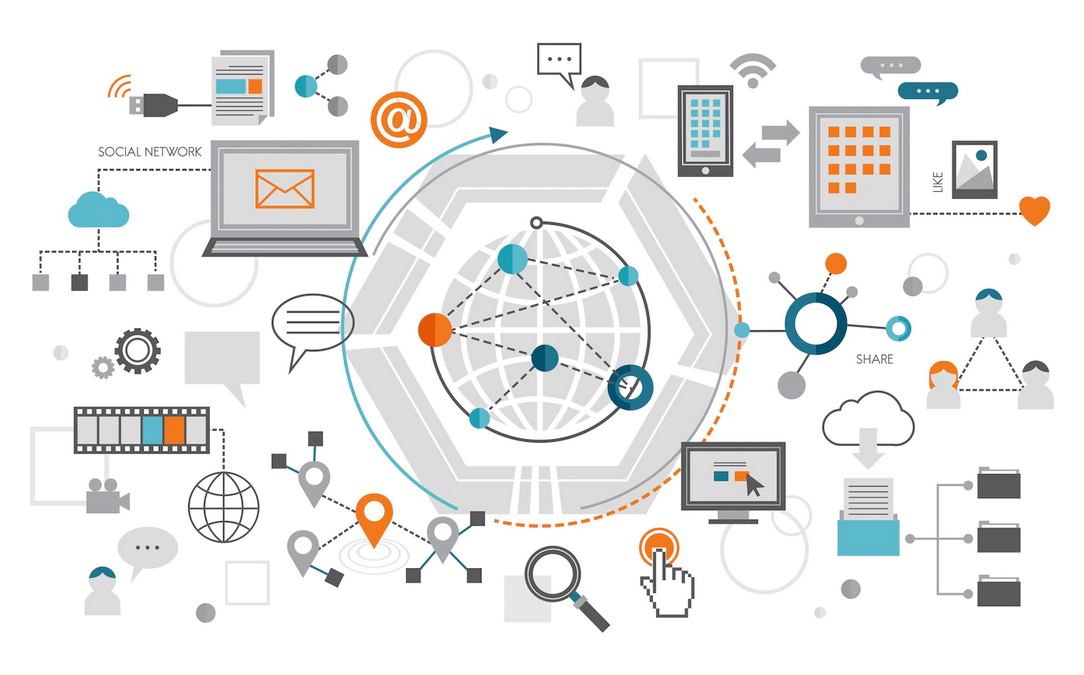
- The wind energy towers are too large to be dipped in the bath
- Corrosion Induced Steel Fabrication
- Preparing a steel structure for galvanising
- Controlling Oxidation of Base Materials with Zinc Spray Coating
- Zinc Coating
- Plasmonic Effect on Materials
- A high-quality acoustic powder for the construction of large objects
- Longevity of Zinc Thermal Sprayed Coating
- Thermal spray technology for coating of zinc
- Preventing the formation of a strong bond between an inorganic zinc-rich primer and its substrate
- What Characteristics Does Zinc Give to Galvanized Steel?
The wind energy towers are too large to be dipped in the bath
The wind energy towers can be too large to be dipped in the bath. Zinc thermal spraying is used to protect steel articles. The hot dip process can be used to coat steel that is difficult to reach, but zinc thermal spraying can be used to coat steel that is already in use.
Corrosion Induced Steel Fabrication
Steel fabrications are always at risk of being attacked by corrosive elements, whether used for structural or architectural purposes. The metal can be damaged by wind, frost and water. The flexibility and cost savings provided to end- users are the ultimate reason for hot metal spray treatment to be used in metal fabrication.
Preparing a steel structure for galvanising
The process of galvanising steel does a good job at protecting it, but it is not safe because the steel is heated to near its melting point. There will be more work for us once the piece gets back from galvanisation. Many times the holes need to be re-drilled and there will be slag.
If you are going to paint your steel structure, galvanising will make it more difficult. Special preparations are needed for paint to adhere to a galvanised finish. The paint needs to stick to the metal so that it can be sanded.
Controlling Oxidation of Base Materials with Zinc Spray Coating
Base materials are protected from oxidation with zinc spray coating. Zinc is more likely to oxidize than other metals. Zinc has a proclivity to oxidize first, so it limits the oxidation of the other metals in contact with it.
Zinc spray coating are not as easy to control as other processes. The coating is typically thicker and less resistant to wear. The operator skill is a big factor in the coating from zinc thermal spray.
Zinc Coating
The metal particles are sprayed onto the roughened surface where they attach to the surface and solidify. The typical coating thickness is between 80 and 300 microns, but thicknesses of 50 to 500 microns are also possible. Mild, low-alloy and high-carbon steels are used in the production of zinc coating.
Plasmonic Effect on Materials
The effects of plasms on materials at an atomic level. Surface analysis using techniques like X-ray photoelectron spectroscopy and scanning electron microscopy can help identify the processes required and to judge their effects. A water droplet contact angle test is used to determine surface energy and wettability. The higher the contact angle, the more surface energy and the more hydra-philic the material is.
A high-quality acoustic powder for the construction of large objects
It can be applied to large items, which is a benefit, as it does not cause distortion, and it can be site applied or touched up. The end use can be varied. The finished material can be overcoated with a variety of finishes. It can be left as is, or it can be overcoated with most paints.
Longevity of Zinc Thermal Sprayed Coating
The most effective method of protection is coating steel with zinc. Zinc coating protects steel by providing a physical barrier and also protects the underlying steel from damage. The application of sprayed zinc is an uncomplicated yet versatile procedure that offers no continuous maintenance, years of lasting protection, and a comparable life cycle, thus ensuring cost savings during the service life of the structure.
Thermal spray technology for coating of zinc
Thermal spray technology uses a low power spray beam between two wires to atomise the wire and turn it into spray stream. The wire is made from zinc and is used in fresh water systems. The process is similar to that of arcs welding where the welder touches the welding rod against the work piece and then withdraws it to form a stable arcs.
The welding rod and work piece are not the same as the wire feedstock in thermal spraying. The coat weight is measured to ensure consistency of coating of around 1 kilogram of zinc per sqm. Smaller pits and scrapes will be filled with a spray coating, resulting in a more aesthetically pleasing end result.
Preventing the formation of a strong bond between an inorganic zinc-rich primer and its substrate
The size of the structure is important when protecting it from the elements. If the asset is small in size, hot-dip galvanizing is the most cost-effective method. Inorganic zinc-rich primers only require blast cleaning and spray pump. The zinc-rich primer can be applied like paint and be ready to ship in less than a minute.
What Characteristics Does Zinc Give to Galvanized Steel?
What characteristics does zinc give to galvanized steel? The characteristics of galvanized steel are given. It gives high strength. It makes steel look better.









X Cancel