What Is Time Quality Management?
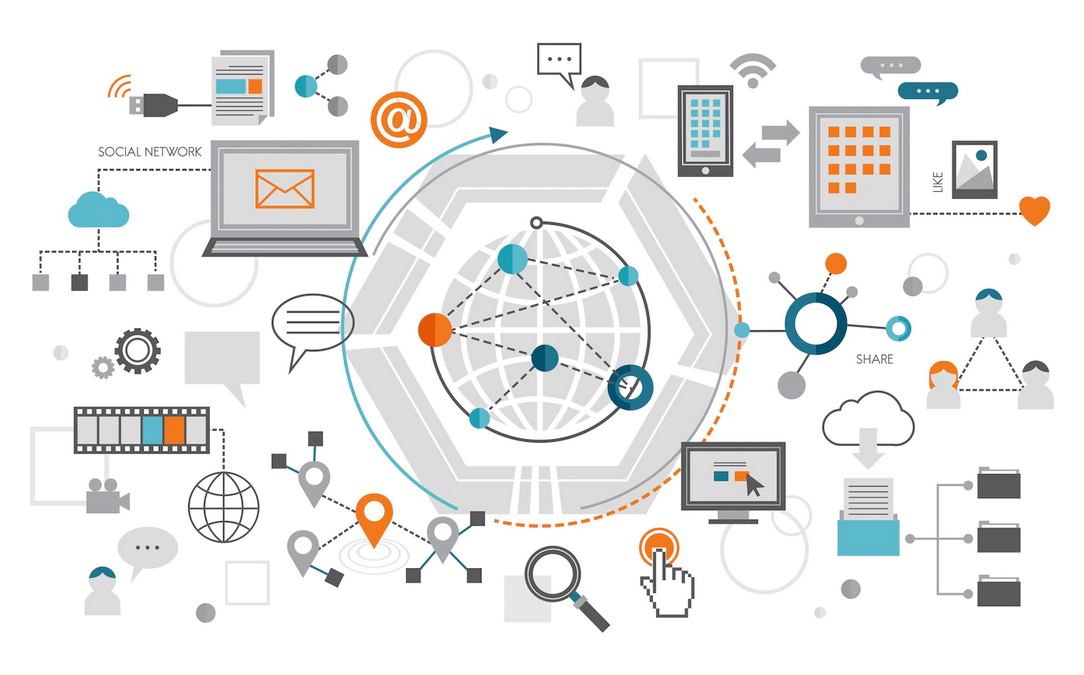
- TQM: A Customer Satisfaction First Approach
- A Case Study of TQM in a Tato Group
- The Project Management Triangle and Quality
- Process of Quality Management
- Statistical Process Control and Function Quality Integration
- Time Management
- Cost-Effective Optimization: A Key to Improved Productivity
- The Role of the Inspectors in Detecting Error
- What is Quality?
- Managing Quality in Manufacturing Organizations
- Total Quality Management: A Conceptual Approach to Continuous Improvement
- Quality Management in Engineering Projects
TQM: A Customer Satisfaction First Approach
TQM is a business philosophy that believes that long-term success of a company comes from customer satisfaction and loyalty. TQM requires that all stakeholders in a business work together to improve processes, products, services and the culture of the company itself.
A Case Study of TQM in a Tato Group
Many organizations have adopted other, more modern management techniques as their needs for efficiency, productivity and quality have further evolved. TQM is still important in some businesses, but other management techniques such as Six sigma and lean manufacturing are more efficient and effective. The company that is an example of TQM is the subsidiary of the Tata Group, called Tata Steel.
TQM was adopted by the steel company. The company was awarded a prize. TQM methodologies were used by the company to gain a deeper understanding of customers.
The Project Management Triangle and Quality
The project management triangle is a useful tool for decision making. It is often used as a joke in training courses. It is a powerful tool that can be used by a leader or professional.
Process of Quality Management
Quality management is the act of making sure that the products and services offered are consistent and that the means used to provide them are. It helps to maintain a desired level of quality. The process of quality management involves a collection of guidelines that are developed by a team to ensure that the products and services that they produce are of the right standards or fit for a specified purpose.
Product improvement, process improvement, and people-based improvement are some of the methods used to improve quality. There are many methods of quality management that can be used. They include the Toyota Production System, Kansei Engineering, and the BPR.
The process approach principle states that the performance of an organization is crucial. The approach principle emphasizes efficiency and effectiveness. Good processes result in improved consistency, quicker activities, reduced costs, and waste removal, and continuous improvement, and the approach entails an understanding that this.
The inputs and outputs of an organization can better managed and controlled by the leaders. Every organization should have an objective to be involved in continuous improvement. Businesses that continually improve experience improved performance, flexibility, and ability to embrace new opportunities.
Businesses should be able to create new processes and adapt to new market situations. Businesses should use a factual approach to decision-making. Businesses that make decisions based on verified and analyzed data have an improved understanding of the marketplace.
Statistical Process Control and Function Quality Integration
The Quality Management Task Force was able to develop an initial framework. The framework of the QM is not a finished product, but a step towards the line of perfect quality. Statistical Process Control is the application of formal statistical sampling and control procedures that allow very accurate monitoring of the process by which a task is performed, thereby ensuring that the product will be in conformance with specifications.
Time Management
Many successful people have different approaches to success. They have the same thing, that they know how to juggle high-level projects and make sure they spend the bulk of their time on the tasks that are most beneficial to their success. Managing your time can affect your stress level.
You will face fewer surprises, have less tight deadlines, and be less rushed. Good time management skills allow you to set aside time each night to get a proper amount of sleep. Getting enough rest can have a big impact on the quality of your decisions and can affect almost every area of your life.
Cost-Effective Optimization: A Key to Improved Productivity
Increased productivity is achieved by cost reduction. Productivity is the maximization of output with optimum utilization of resources. The quality of resources, infrastructure, high-end technology and competent employees increase productivity.
TQM brings in tangible results like superior product quality, reduction in costs, increased profitability, and productivity. Improved communication, teamwork, employee engagement, customer satisfaction, goodwill, and increased employee morale are some of the intangible returns. TQM requires employees to go through a lengthy training period, participate in quality improvement and be involved in the company.
The Role of the Inspectors in Detecting Error
The inspectors have the authority to stop production if they detect an error. If they have to, they can stop the production line until the problem is fixed. It is important that everyone knows what the activities are.
What is Quality?
Natural characteristics that can't be separated from something are inherent. ISO does not agree with the term inherent to assigned and defines inherent as existing in something. Quality should be defined in a way that it can be managed.
The definition of quality depends on your perception of the scope of quality management. If all cars have the same number of wheels, it is not a distinguishing feature of the car. The number of wheels of a 5 wheel car is a distinguishing characteristic which is consistent with the ISO 9000 definition.
Managing Quality in Manufacturing Organizations
If all of the organization's members focus on improving quality, it will be able to build long-term growth and success. In the United States, 14 percent of manufacturing firms use TQM. It can be applied to a variety of industries. You can integrate with thousands of apps through Zapier, webhooks, orAPI integration, and you can create templates and run individual checklists from them to manage all your recurring tasks.
Total Quality Management: A Conceptual Approach to Continuous Improvement
The Total Quality Management approach focuses on continuous quality improvement of products and services offered by the firm by using continuous feedback. The founder of Total Quality Management was Joseph Juran. The concept of Total Quality Management was developed in Japan in the year of 1954.
Industry standards can be defined at multiple levels and may include adherence to various laws and regulations. Even if the production of items is not backed by official rules and regulations, industry standards can include it. It strives to ensure that all employees work towards the same goals of improving product and service quality, as well as improving the work procedures that are in place for the production process.
It is important to remember that only customers decide the level of quality of the products and services when using Total Quality Management. Customers only determine whether your efforts have contributed to the continuous improvement of product quality and services or not, by evaluating your efforts with respect to training employees or improving the work processes. Continuous improvement proposals will be initiated and implemented if the organization uses the right measuring tools and innovative and creative thinking strategies.
Quality Management in Engineering Projects
Reports from Business Roundtable, American Society for Quality Control, the government and others are making owners and management more aware of the pressures for better quality and cost effectiveness in engineered projects. The project must be concept stage before it is turned over to engineering and construction. Quality must be managed in the two final stages.
6. The project people will benefit from having physical scale models of the facility to aid in their visual aid. The models will show interferences, potential hazards and potential production problems if they are present.
Quality management from the Project Manager's perspective is not limited to quality of materials, machines and installations. Corporate management level development and support of attitudes toward quality and cost effectiveness is where quality management begins. The newest apprentice in the group must be communicated those attitudes down the corporate ladder.









X Cancel